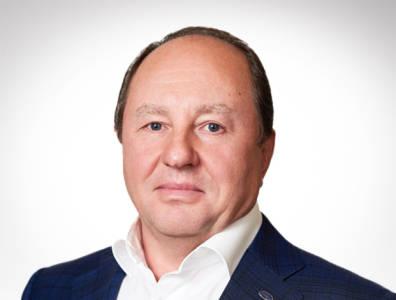
Innovation and automation in Russian rigs
March 31, 2020Yuri Karpov, general director of Uralmash Oil and Gas Equipment Holding (Uralmash NGO Holding), talks to The Energy Year about demand in the Russian drilling rig market and how the company is advancing the design of its rigs. Uralmash NGO Holding manufactures drilling rigs for drilling deep production and exploration wells.
This interview is featured in The Oil & Gas Year Russia 2020
How did demand in the Russian drilling rig market develop in 2019?
The demand in the drilling rigs market in Russia depends on many factors. First, it depends on macroeconomic factors, mainly the price of oil. When the oil price drops, volumes of drilling decrease.
Moreover, there has been a sort of cyclical evolution over the past five years. In 2019, the demand for drilling rigs was approximately 30% lower than in 2018. But in 2018, the demand for drilling rigs was 29% higher than it was in 2017. So even if there are significant changes year-on-year, the demand was quite stable on average over this period.
There are some tendencies that influence these conditions. A little more than 1,000 drilling rigs are operated in Russia. One third of these are technologically and physically exhausted.
Subsoil users are increasing requirements for drilling companies. Drilling companies, with their old drilling rigs, are no longer able to fulfil all of the demands of subsoil users. So they have to purchase new equipment, which raises the requirements and sets new tasks for us. There are many requirements coming from customers, such as for automation and innovative solutions.
Do you expect an increase in demand in 2020?
Knowing the demand of large oil and gas production companies – such as Gazprom, Rosneft, Novatek and Surgutneftegas – an increase in growth is foreseeable. As the drilling rigs are pretty worn out, the drillers are faced with quite serious tasks to upgrade this fleet, based on requirements to increase penetration and increase mechanical and commercial speeds. Today, customers demand an increase in the rigs’ hook-load capacity and the high hydraulic power of mud pumps. This is why we are producing new mud pumps with higher hydraulic pressures.
How has the company achieved growth in the 10 years since its foundation?
The company is celebrating its 10th anniversary in 2020. Ten years does not seem like a long time. It all started with an office in Moscow and a factory in Yekaterinburg – the URBO plant. When you operate only one plant, there is only one system to manage.
But in these 10 years, the company has acquired two more production sites: the BKU plant in Tyumen and the Neftemash plant in Otradny. Tyumen is a geographically convenient place for delivering our equipment to North-West Siberia and East Siberia, where most of the drilling works are carried out. We can ship our equipment from Tyumen by railroads, roads and rivers. This is why we acquired this plant.
We also created a service company called Uralmash-Techservice (offices in Moscow, Yekaterinburg and Buzuluk). The main service and production branches are located in the regions where customers operate throughout Russia. We also expanded our engineering capacities through the acquisition of the Volgograd company Neftegazengineering.
What is the production capacity of your main facilities?
In the beginning, our plant in Tyumen produced 5,000 tonnes of equipment per year. In 2019, the factory produced 16,000 tonnes. We plan to raise production volumes in this factory up to 22,000 tonnes per year.
When we acquired the Neftemash plant, it produced about 2,000-2,500 tonnes per year of drilling equipment. Now it produces about 4,500 tonnes of commercial products.
What were Uralmash’s main achievements in 2018 and 2019?
In the last few years, the holding has been developing dynamically. In 2018-2019, we produced 40 drilling rigs.
During this period, the company designed and started the production of top drives with load capacities of 250, 320, 450 and 500 tonnes.
In the past two years, we have also increased the production of serial UNBT-1180L mud pumps (1,600 HP) with a pressure of 35 MPa (5,000 psi). Also in our product line we have mud pumps with a capacity of 1,600 HP and 2,200 HP with the pressure 52 MPa (7,500 psi).
What is your market share in Russia?
Currently, the share of Uralmash NGO Holding in the Russian market of heavy drilling rigs is 55-60% both in value and in volume.
What automation solutions have you introduced in Russia recently?
First I would like to say that our drilling rigs are of block-modular design and equipped with a variable speed AC drive with frequency regulation. The AC drive motors are powered by diesel-electric units or by high-power lines through a container-type VFD assembly. Drilling rigs are completed with a driller’s cabin, equipped with ventilation and an air-conditioning system. Drilling rigs are equipped with a single- or two-speed high performance draw works, triplex mud pumps.
Drilling rigs manufactured by our company are a computerised complex, which is controlled from the driller’s cabin through joysticks and touch screens. The proprietary top drive and proprietary drilling rig control system software as well as other systems increase the operational characteristics of the drilling rig and improve the working conditions of the drilling crew personnel.
We have significantly improved the automatic control system (ACS). All drilling operations at our drilling rigs are controlled by the ACS system. A lot of changes were made in terms of accident warning and tracking equipment performance. All the drilling rigs that we produce today are equipped with top drives. The drilling rigs’ design allows for negative environmental effects to be minimised. All of these innovations were developed by our engineering centre.
In September 2019, Uralmash NGO Holding delivered a drilling rig to Eriell. What were the technical requirements set by your client?
Indeed, this rig has been manufactured. We put it into operation at the beginning of 2020. There were very few difficulties in this project because we have previously produced a similar drilling rig of Arctica type, which is already in operation.
The main requirement of the customer was to minimise the costly downtime of rig equipment due to weather conditions. The task was to create a drilling rig that could drill in the harshest conditions of the Far North with temperatures up to -60°C and a strong, gusty wind.
What are the specifications of Arctica rigs?
The drilling rig BU 6000/400 EK-BMCh, supplied to Eriell Neftegazservice, is a unique development of Uralmash NGO Holding, which has no domestic counterparts in the drilling equipment market.
As a result, a modification of the commercially available drilling rig BU 5000/320 EK-BMCh was created. The carrying capacity has been increased, a combined heating system, a shelter for the derrick, heating working platform, as well as a sheltered and heated pipe workshop have been installed. The double echelon makes it possible to move the entire complex from well to well without dismantling the equipment and the pipe shop. The main emphasis in the design of this drilling rig was made to increase the safety and comfort of the drill, as well as to minimise the downtime required by the customer due to severe weather conditions. All this together will give an additional economic benefit to the drilling company from the use of this drilling rig.
Did you customise the drilling rig you delivered to Eriell in September 2019?
As such, there were no difficulties in the implementation of this project. The only difficult task was to develop a set of shelters for use on a typical drilling rig, which is produced by the holding serially. This task was successfully solved by our designers, and now this project can be replicated for almost any of our EK-BMCh series drilling rigs.
Now we are preparing to ship another drilling rig of this type for Eriell.
Uralmash NGO Holding signed a contract for supplying a drilling rig to Glencore in June 2018. Have you completed this project?
Glencore was in fact only a financial intermediator in this project. The final customer was a drilling company called RussIntegral-Pioneer. We finalised this project in November 2018. It took us only six months to supply the drilling rig to the oilfield. We completed this project in such a short period of time thanks to the early pre-manufacturing programme that we implemented in 2014.
This system consists of a preliminary production of drilling rigs that are stored in our warehouse. Knowing the market and the requirements of our clients, we produce and store from five to 20 drilling rigs at our warehouse. After we sign a contract for the supply of a rig, it takes us not more than six months to ship it, whereas the production of a new rig can take up to nine months. This system has provided us with a competitive advantage, and it is convenient for our customers.
How was the purchase of this rig financed?
Glencore financed the purchase of the rig through leasing. Today, almost 90% of companies use a leasing purchase scheme. This is a more convenient and flexible system for them. We work with many leasing companies, including Glencore, Gazprombank Leasing, VTB Leasing, Sberbank Leasing and many others. In addition, the Industrial Development Fund for Russian companies has a programme of preferential loans for advance payments for oil and gas equipment purchased on lease, which makes leasing even more attractive.
Do you get support from the government to develop import substitution solutions?
We were influenced by sanctions, which gave impetus to the development of import substitution. Five years ago, the share of imports was about 40% of the Russian market. Now this share is about 5-7%. The state is working on a variety of import substitution programmes. They support our research and development (R&D) programmes. Right now, together with the state we are working on a recycling programme.
How important is your URBO plant’s API certificate? Did you get it to extend your supply abroad?
American Petroleum Institute (API) certification is required to enter overseas markets. The presence of API certificates is a mandatory requirement for all manufacturers of drilling equipment participating in tender procedures in foreign oil and gas and drilling companies. Therefore, of course, we deliberately passed this certification in order to supply products to foreign markets and confirm that our quality and product management system complies with API specifications.
Drilling companies operating in Russia do not require API equipment certificates from the equipment manufacturer. Nevertheless, this certification contributed to building the optimal quality management system in our company, which undoubtedly affected the improvement of the company’s management system, the increase in labour productivity and customer satisfaction, thereby increasing the company’s competitiveness in the market.
What regions do you target as a priority?
In the West, in Europe and the USA, as well as in China, there are many in-house drilling rig manufacturers. We know them all. I have visited almost all of their factories. Due to strong competition in these countries and regions, we do not consider them a priority.
We are now focused on the Middle East and Latin America. We negotiate with customers there. In these countries, there is a great demand for our equipment. That is why the markets of these countries are interesting for us.
What are your competitive advantages on the international market?
Our first advantage is the price. The price of equipment is the main factor in the market today. We are competing with Chinese rig manufacturers on the international market, of which there are many. They are the only ones we compete with in terms of price of equipment.
How are Chinese manufacturers developing in Russia?
The market is open for them. Chinese manufacturers supply their equipment to Russia, but do not have their own production facilities in Russia. We successfully compete with Chinese companies in the drilling rig segment with a carrying capacity of more than 200 tonnes. Our share in the Russian market is greater than theirs. However, we are not very strong in lightweight mobile drilling rigs with a lifting capacity of up to 200 tonnes, while the Chinese are very strong in this segment.
What are your plans for the future?
We plan to build offshore drilling rigs. This has been our dream for a long time, and it is feasible.
As for onshore projects, we plan to continue with innovations and automation. Our engineering centre is working on these now. We have already set an R&D programme for 2020. The programme includes designing and manufacturing a self-assembling drilling rig. This is a rig that can be assembled on a well pad without any cranes.
This enables the customer to reduce their operating costs. They will not have to haul any cranes to assemble the rig. They will only have to deliver it to the oilfield, and it will assemble and disassemble itself. We have already received interest and support from our customers.
Another prospective development is a gearless top drive. Now we are finishing the design documentation and plan to bring this top drive to the market by the end of 2020.
What is your development plan to increase and improve your production in the coming year?
In 2019, we completed a RUB 4.3-billion [USD 70.1-million] investment programme. Now we will implement our next one. This investment programme provides for the modernisation of our production facilities. That allows you to increase the volume of products by increasing productivity through the introduction of the latest technology and improve the quality of products.
A contract for the supply of two metal-processing complexes of the leading Austrian WFL equipment is underway. These complexes allow us to increase the production of shafts, pumps, winches and top drives through the use of new manufacturing technologies.
The plans include the purchase of an ion-nitriding complex, which will allow us to achieve the best results of hardening the surface of the gears. We are also going to purchase a control and measuring machine, which will allow us to control the smallest deviations in the production process.
We are also upgrading the old metal cutting machines.
Are you planning some changes in the organisation of your industrial production?
Presently we have adopted a programme to systematise and unify our production process. It is necessary to bring all processes to common standards and parameters to manage the holding’s plants. This is a difficult job involving great responsibility.
At the moment, we are focusing on the development of machining at our BKU plant. And we are planning to make a powerful assembly site at the URBO plant.
We plan to complete this process in stages in two years and to reach a new level of our products in 2022 and 2023.
Read our latest insights on:
-
-
Support at every step
INTERVIEW -
Potential in Russia’s Arctic
INTERVIEW
More content from Russia
Building on fictional content
InterviewWorking with Useful Services
Viewpoint